In modern warehousing and logistics management, the Dock Leveler is one of the core equipment to ensure efficient and safe operations. Whether in the process of transporting goods or in daily loading and unloading operations, dock levelers play a crucial role. They bridge the height difference between the lorry and the warehouse, ensuring that goods are loaded or unloaded smoothly and safely.
For different warehouse needs, there are many types of loading platforms available on the market, of which Mechanical Dock Levelers and Vertical Dock Levelers are the two most common. Each has its advantages and disadvantages, with differences in operation, cost, efficiency, durability, and safety. Therefore, when choosing the most suitable dock leveler, it is important to understand its characteristics, application scenarios, and long-term maintenance and usage costs.
In this article, we will compare these two types of loading platforms in detail to help you make the most suitable choice for your specific needs, so as to improve the efficiency of your warehouse operations, reduce costs and enhance safety.
Understanding loading docks and their importance in the warehouse
In modern warehouses and distribution centers, loading docks are not only a tool to ensure smooth material handling, but they also have a direct impact on the efficiency and safety of the warehouse. Mechanical loading platforms and vertical loading platforms are two common types of loading platforms, each of which has its characteristics and is suitable for different warehouse and logistics needs. Choosing the right loading and unloading platform can help companies improve operational efficiency, reduce operating costs, and ensure personnel safety.
Whether it’s a traditional mechanical loading platform or a more modern vertical loading platform, they all work together to provide a smooth transition and eliminate height differences during loading and unloading.
Mechanical Handling Platforms: Overview and Application Scenarios
Overview of Mechanical Dock Levelers
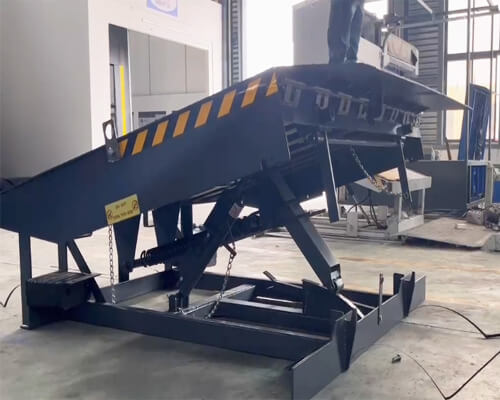
A Mechanical Dock Leveler is a manually operated loading and unloading platform, usually consisting of mechanical components such as springs, levers, or chains. It is simple in design and robust in structure, and operates entirely by hand, adjusting the height of the platform by pulling a chain or lever to ensure that the platform is docked with the transport vehicle. Although its operation is more laborious, it is still widely used in low-frequency environments due to its low price and simple maintenance.
Application Scenarios for Mechanical Loading Platforms
Mechanical loading platforms are usually used in the following places:
Warehouses with low-frequency operations: Suitable for warehouses and small distribution centers where loading and unloading are less frequent. For example, small retailer warehouses or large distribution centers that handle fewer goods.
Small businesses with limited budgets: For companies with limited budgets, mechanical loading platforms offer a cost-effective solution.
Gentle working environments: Due to their simplicity, mechanical loading platforms are generally suitable for gentler operating environments that are not subject to extreme weather or high loads.
Whilst mechanical loading platforms are simpler to operate, they have a relatively limited load capacity and frequency of use, making them suitable for less demanding warehouse environments.
Vertical Loading Platforms: Overview and Application Scenarios
Overview of Vertical Dock Levelers
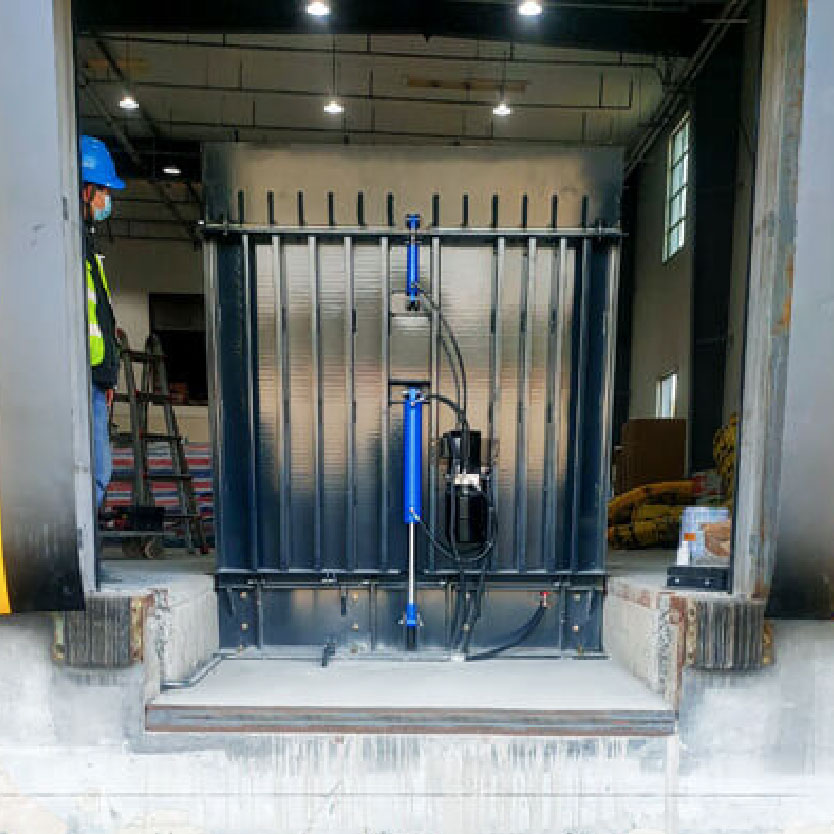
Vertical Dock Leveler is a kind of automated equipment, usually driven by an electric drive system or hydraulic system, which can adjust the height of the platform by push button or remote control. Compared to traditional mechanical platforms, the Vertical Dock Leveler is fully automated and can be quickly and smoothly adjusted in height to suit different vehicle access requirements. These platforms are particularly suitable for warehouses and distribution centers with high-frequency and high-intensity operations.
Vertical loading and unloading platforms can be partially raised vertically to maintain high load capacity and stability, especially suitable for environments that require high efficiency and safety.
Comparison Dimension | Mechanical dock leveler | Vertical dock leveler |
Operating Mechanisms | Manual operation (chain/lever) | Fully automatic (electric/hydraulic drive) |
Initial Cost | Low (no complex power system) | High (with hydraulic/electric system) |
Long-term cost | High labor costs (low efficiency in high frequency use) | High maintenance cost but labor cost saving |
Load capacity | Medium (typically ≤ 10 tons) | High (up to 15 tons or more) |
Adjustment speed | Slow (dependent on human labor) | Fast (0.6-1.2 m/sec) |
Security | Dependent on manual operation, high risk | Equipped with sensors, automatic locking, overload protection |
Applicable Scenarios | – Low frequency operation- Small warehouse- Limited budget | – High frequency/high load operation- Large logistics centers- Automated warehousing system |
Maintenance Requirements | Simple (lubrication/cleaning of mechanical parts) | Complex (requires regular inspection of hydraulic oil, circuit system) |
Installation Complexity | Low (no electrical connection required) | High (requires specialized technicians to install power systems) |
Environmental Impact | Low energy consumption (no power dependency) | High energy consumption (requires continuous power supply), but efficient operation can reduce overall resource waste |
Typical Industries | Retail warehousing, small distribution centers | E-commerce logistics, manufacturing, cold chain centers |
Application Scenarios of Vertical Loading Platforms
Vertical loading platforms are widely used in the following places:
Warehouses and logistics centers with high-frequency loading and unloading: Vertical loading and unloading platforms are especially suitable for large warehouses, logistics centers, and distribution stations that require frequent loading and unloading. For example, e-commerce warehouses, cold chain logistics centers, and fast-flowing production workshops.
Large Industrial Facilities: Vertical platforms have a strong load-bearing capacity and are suitable for the transport, loading, and unloading of heavy goods, especially in manufacturing, auto parts production, and warehousing of large machinery and equipment with important applications.
Places requiring automated operation: vertical loading and unloading platforms have a high degree of automation, reducing manual intervention, so they are particularly common in modern warehousing and automated logistics systems.
Vertical loading and unloading platforms have become common loading and unloading equipment in modern warehouses and logistics centers due to their high efficiency and safety, especially suitable for large-scale operations and high-load environments.
Comparison of Operating Mechanisms: Manual vs Automated
Mechanisms of mechanical handling platforms
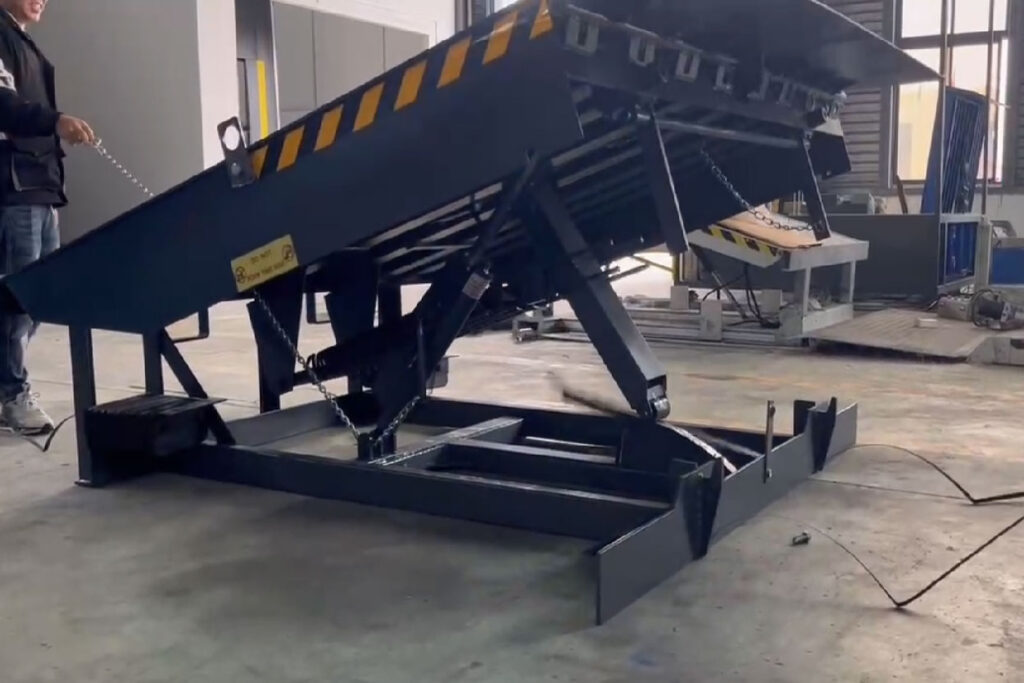
Mechanical dock leveler has a relatively simple operating mechanism, relying on manual labor. Workers pull a chain or lever to adjust the height of the platform to suit different vehicles. The platform’s simple design and lack of electrical support means there is no need to worry about power failures or maintenance of the hydraulic system.
However, manual operation also means that each loading and unloading requires a certain amount of time and effort investment. Especially in high-frequency operations, manual operation may lead to a decrease in efficiency and even increase the safety risks caused by operational errors.
Operation mechanism of vertical platform
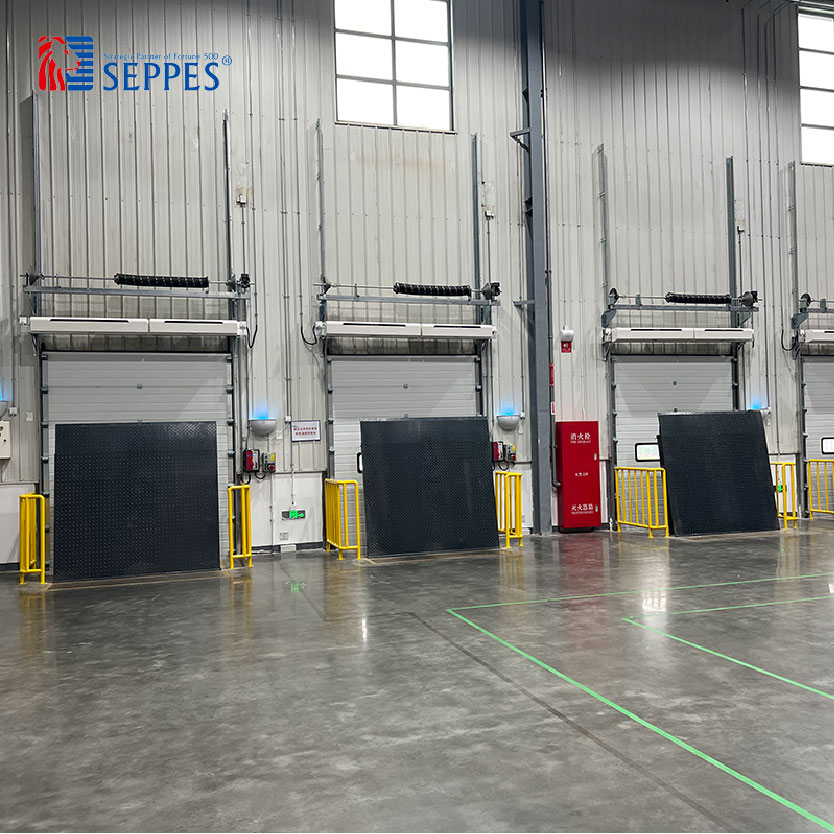
Vertical loading and unloading platform adopts automation control and quickly adjust the height of the platform through the electric or hydraulic system. The operator only needs to press a button or use a remote control. The platform can be automatically lifted and lowered to quickly adapt to the height requirements of different vehicles. This automated operation reduces reliance on manual labor, greatly improves efficiency, and reduces the risk of operator error.
Vertical loading platforms are more flexible than mechanical loading platforms and are suitable for environments that require frequent and efficient operations, especially in large-scale, high-intensity workplaces.
Cost comparison: which platform is more cost-effective?
Cost of mechanical handling platforms
The initial investment in a mechanical loading platform is usually low due to its simple construction and the fact that it does not require an electrical or hydraulic drive. This makes it ideal for smaller warehouses or low-frequency operations with limited budgets. In addition, maintenance costs for mechanical platforms are also low, usually requiring only regular inspection and lubrication of mechanical components.
However, despite the low initial investment, for high-frequency use environments. Mechanical loading platforms may have higher long-term operating costs due to the inefficiencies and labor costs associated with their manual operation.
Costs of Vertical Loading Platforms
Vertical loading platforms have a relatively high initial investment, especially if hydraulic and electric drive systems are required. Installation and maintenance costs are also relatively high, as they require regular inspections of the hydraulic, electric drive, and control systems. Nonetheless, due to their high level of automation, vertical loading platforms are able to increase efficiency in high-frequency operating environments, thus saving companies labor and time costs in the long run.
Safety comparison: which platform is safer?
Safety of mechanical loading platforms
The operation of a mechanical loading platform requires workers to manually adjust the platform, which may increase the risk of human error. Although it is a simpler design, frequent manual operation may lead to worker fatigue. Which increases the likelihood of accidents, especially when improper operation may lead to platform failure or injury.
Safety of vertical loading platforms
Vertical loading platforms offer increased safety through automated operations and safety sensors. Many modern vertical loading platforms are equipped with automatic locking features, overload protection. And safety sensors to ensure that unnecessary accidents do not occur during the loading and unloading process. Automation reduces the risk of human error, especially in high-frequency environments.
Comparison of environments: Which platform is better for your warehouse?
Mechanical loading and unloading platforms
Low-frequency operation: suitable for warehouses with low loading and unloading frequency.
Small business with limited budget: low initial investment, suitable for places with limited budget.
Gentle operating environment: suitable for non-high-load, high-frequency operation sites.
Applicable environment of vertical loading and unloading platform
High-frequency, large-scale loading and unloading operations: suitable for warehouses and distribution centres that require efficient, frequent loading and unloading.
High-load environment: applicable to large-scale operations such as heavy goods and mechanical equipment.
Automated warehousing: suitable for modern warehousing and logistics systems that are highly automated and require less manual operation.
Maintenance vs. maintenance: which platform is easier to maintain?
Maintenance of mechanical loading platforms
Mechanical loading platforms have a simple structure and low maintenance costs. Typically, maintenance mainly consists of cleaning, lubrication, and regular inspection of mechanical components. However, frequent manual operation and wear and tear can lead to damage to the components and regular inspections are required to ensure the platform’s proper operation.
Maintenance of Vertical Loading Platforms
Vertical loading platforms require higher maintenance because they include hydraulic and electric systems. Hydraulic oil levels, electric drive systems, and control modules need to be checked regularly. Despite its higher maintenance cost, its high efficiency and automation can reduce manual operations and improve the overall efficiency of the warehouse in the long run.
Installation process: which platform is easier to install?
Mechanical Dock Leveler
Mechanical loading platforms are simpler to install and usually do not require complex electrical or hydraulic connections. They are suitable for smaller warehouses, are quick to install, and are suitable for businesses with limited budgets.
Vertical Dock Leveler
Vertical loading platforms are more complex to install, requiring electrical and hydraulic connections, and may require specialized technicians. Although they take longer to install, once installed they provide a more efficient and safer loading and unloading experience.
Environmental impact: which platform is greener?
Mechanical Dock Leveler
Mechanical loading platforms do not require electrical power, so they consume less energy and have a lower environmental impact, making them suitable for environments where energy conservation and environmental protection are important. Due to their simple design, mechanical platforms require less energy and can reduce operating costs.
Vertical Dock Leveler
Vertical loading and unloading platforms require electric or hydraulic drive and therefore have high energy consumption. Although they consume more energy initially, their efficient performance and automated operation can reduce the energy consumption of other equipment. And in the long run, their high efficiency helps to reduce energy waste.
Conclusion: Which loading dock is right for your warehouse?
Low-Frequency Use: If your warehouse has a low frequency of loading and unloading, a mechanical loading platform is a cost-effective option for smaller warehouses with limited budgets.
High Frequency Use: For high frequency, high intensity loading and unloading operations. A vertical loading platform will provide greater efficiency, safety and long term return on investment.
Choosing the right loading dock will bring significant long-term benefits to your warehouse management. Considering the different needs of loading and unloading frequency, budget and working environment, make the most suitable choice to ensure your warehouse operation is efficient and safe.
Frequently Asked Questions (FAQ)
What is a mechanical loading platform? What environments is it suitable for?
Answer: A mechanical dock leveler is manually operated loading and unloading equipment suitable for warehouses with low-frequency use and small businesses with limited budgets. It is suitable for mild operating environments and is less costly, but is not suitable for high-frequency operations.
What is a vertical loading platform? What are its advantages?
Answer: Vertical loading platforms are automated equipment with height adjustment using an electric or hydraulic system. It is suitable for high-frequency, high-intensity warehouse operations, providing greater efficiency and safety and reducing the need for manual handling.
Which platform is better suited to my warehouse’s needs?
Answer: If your warehouse has a low frequency of loading and unloading and a limited budget, a mechanical loading platform may be more suitable. If you need high-frequency, high-efficiency loading and unloading operations with unlimited space, a vertical loading platform is a better choice.
Can vertical loading platforms carry heavy loads?
Answer: Yes, vertical loading/unloading platforms are suitable for heavy cargoes and can withstand large loads. Which is especially suitable for manufacturing and heavy machinery and equipment warehousing operations.
Do mechanical loading and unloading platforms need regular maintenance?
Answer: Yes, mechanical dock leveler require simple cleaning and lubrication regularly to ensure their smooth operation. Compared to vertical loading platforms, maintenance requirements are lower.
Is the installation of a vertical loading platform complicated?
Answer: The installation of vertical loading platforms requires the connection of hydraulic and electric systems. Which usually require professional personnel to install, and the installation process is relatively complicated.