Sectional doors in the industrial special room in modern industrial production, the special environment of the industrial door system puts forward high requirements. Strongly corrosive pickling liquids in pickling rooms, paint dust and flammable gases in baking and spraying rooms, as well as high-speed splashing of sand in sandblasting rooms pose a serious challenge in terms of door materials, sealing performance, and safety protection.
The sectional door’s customized solution not only meets these requirements but also extends the service life of the equipment and reduces maintenance costs through the use of advanced materials and multi-layer protection. In this article, we will analyze in detail the technical parameters and applications of sectional doors in three major industrial environments, and introduce the corresponding replacement program to help purchasers and engineers in the selection on a scientific basis. Application Scenario Analysis — Acid Cleaning Room, Drying and Spraying Room, and Sand Blasting Room Case Details
Basic structure and advantages of sectional door
Basic structure introduction
分节门 adopts a sectional combination structure design, each door panel can be installed and maintained independently. Its main components include:
Door panel: The standard door panel usually adopts a 0.45mm color steel plate. And can also be customized with aluminum alloy or 304 stainless steel, filled with high-density polyurethane foam, to achieve the effect of heat insulation. The overall thickness of the door panel is 40mm, and the height of a single door panel is 500mm
Connectors and hinges: usually adopts high-strength stainless steel or anticorrosive treatment of the metal, to ensure the durability of the long-term operation.
Seals and auxiliary parts: improve the overall sealing performance, preventing the intrusion of external substances.
Technical Advantages
高效开启和关闭: modular design makes sectional doors operate quickly, suitable for frequently used industrial scenarios.
Convenient Maintenance: The structure is designed for easy local replacement and upgrading, reducing long-term maintenance costs.
Multi-protection: Through the internal and external layered design, PVC, rubber, and sealant. And other auxiliary protective materials can be added according to the actual needs to improve the anti-corrosion and dustproof performance.
Detailed Analysis of Application Scenarios and Replacement Solutions
In the following, we propose customized protection solutions for sectional doors for pickling rooms, drying and spraying rooms, and sandblasting rooms, respectively, and introduce replaceable industrial door solutions in accordance with actual needs.
Application of sectional door for pickling room

Customized protection solution
Application background:
The acid-washing liquid in the pickling room is highly corrosive, in order to prevent the liquid from eroding the door plate and hinges, it is necessary to build a multiple protection system.
Design solution:
Inside protection:
Stainless steel inner plate: 304 stainless steel is used as the protection material for the inner side of the door to ensure that it will not rust when exposed to the pickling liquid for a long time.
Stainless steel hinge: all connecting parts use stainless steel to enhance corrosion resistance.
Outside support:
Color steel plate outer layer: 0.45mm color steel plate is used to ensure the stability of the overall structure, taking into account the cost and strength.
Built-in protection layer:
PVC door curtain: A PVC door curtain is added behind the stainless steel inner plate to further isolate the direct contact between pickling water and the metal surface, thus prolonging the service life of the door plate and hinge.
Core Advantage:
The multi-layer protection design provides both internal and external protection. This not only ensures mechanical strength but also significantly reduces the risk of acid pickling solution erosion on critical components. Detailed analysis of application scenarios and replacement solutions
In the following, we propose customized protection solutions for sectional doors for pickling rooms, drying and spraying rooms, and sandblasting rooms respectively, and introduce replaceable industrial door solutions in accordance with actual needs.
Application of sectional door for pickling room
Replacement Solution: Spiral Rapid Door Combination Solution
Replacement Idea:
In some pickling room environments, to achieve faster opening and closing speeds, and to minimize liquid exposure time. A high-speed spiral door can be selected, but requires the addition of a combination of designs with similar PVC protection.
Implementation:
Choose a spiral speed door and increase the opening speed to 0.8-1.5 m/s.
Add PVC protection to the inner side of the door as well to ensure corrosion protection.
Comparison advantage: A high-speed switch can quickly isolate the environment; the disadvantage is that the high-speed spiral door material with long-term corrosion resistance may be slightly inferior to the customized stainless steel sectional door program.
Sectional door solution for baking and spraying room
Customized protection solution
Application background:
The working environment of the baking and spraying room contains a large amount of spraying dust and flammable gases, which have high explosion-proof requirements, and the door body must ensure high sealing.
Design solution:
Explosion-proof electric control system:
Integrated and certified explosion-proof electric control equipment. To ensure that the operation process will not cause an explosion due to sparks.
High sealing design:
Uses a high sealing type, and the four sides of the door body are equipped with EPDM rubber strips, forming a tight barrier to block dust and flammable gases.
Material selection:
Standard color steel door panels can also be made of aluminum alloy to improve corrosion resistance. And filled with high-density polyurethane foam to ensure thermal insulation and structural stability.
Core Advantage:
This solution combines explosion-proof electric control and high-sealing door design. This provides all-around safety protection for the drying and spraying integrated room and ensures the stability and safety of the operating environment. Replacement: Rigid Rapid Door Combination
Replacement Idea:
In some pickling room environments, to achieve faster opening and closing speeds to reduce the liquid exposure time. High-speed roller shutter doors can be used, but need a combination of designs similar to the PVC protective layer.
Implementation:
Choose a rigid speed door and increase the opening speed to 0.8-1.5 m/s.
Add PVC protection to the inner side of the door as well to ensure corrosion protection.
Comparison advantage: A high-speed switch can quickly isolate the environment. The disadvantage is that the high-speed rolling door material with long-term corrosion resistance may be slightly inferior to the customized stainless steel sectional door program.
Replacement Solution: Fire Rapid Door Option
Replacement Idea:
For baking and spraying environments with higher fire protection requirements, fire-rated roll-up doors can be selected to replace sectional doors in some areas to provide an additional fire barrier.
Implementation:
Adopt a higher fire rating door design with explosion proof equipment and high seals.
Comparison: Fire-rated speed doors are superior in fire performance. But it may differ from sectional door options in terms of customization and ease of maintenance.
Sectional door solution for sandblasting room
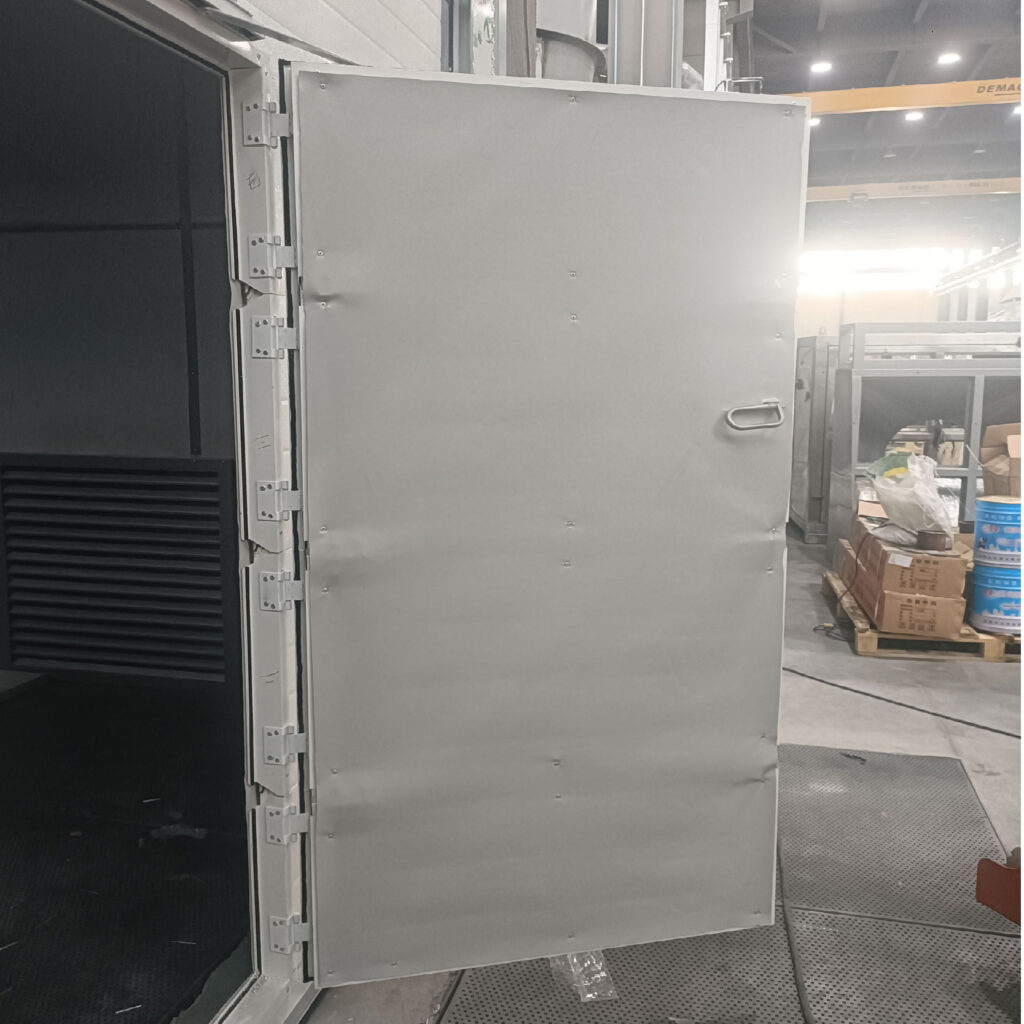
Customized protection solution
Application background:
In the sandblasting room, the high-speed splash of sandblast is easy to directly impacts the door plate, resulting in wear and structural damage.
Design solution:
Built-in PVC protection layer:
Add a layer of PVC door curtain on the inside of the sectional door. It is wear-resistant and corrosion-resistant, and can effectively block the direct impact of abrasive pellets on the metal door plate.
Reinforced structure:
Adopts high-strength metal as the main plate, together with an anti-abrasive coating treatment to enhance the impact resistance.
Core Advantage:
Multi-layer combination of protection design can effectively reduce the damage of sandblasting on the door body. And PVC protection layer replacement cost is low and easy to maintain. Replacement: Fire Rapid Door
Replacement Ideas:
For baking and blasting environments with higher fire protection requirements, fire shutter doors can be selected to replace sectional doors in some areas to provide an additional fire barrier.
Implementation:
Adopt a higher fire rating door design with explosion proof equipment and high seals.
Comparison: Fire-rated speed doors are superior in fire performance, but may differ from sectional door options in terms of customization and ease of maintenance.
Replacement: Rigid Rapid Door Combination Program
Replacement Idea:
In the sandblasting room scenario, if you require the door to open and close quickly. You can consider using a high-speed spiral door. But you also need to add a PVC protective layer on the inside to protect against the effects of sand.
Implementation plan:
Choose a high-speed roller shutter door, in the sandblasting operation gap to achieve rapid opening and closing;
Add built-in PVC protective film, and the door plate to form a double protection;
Comparison of the advantages and disadvantages: spiral fast door response speed. But the overall abrasion resistance and long-term impact resistance may not be as good as the customized sectional door program.
Comprehensive Comparison and Purchasing Strategy
Comprehensive Application Scenarios Comparison Table
The following table summarizes the keys to sectional door customization and replacement solutions in the three major scenarios of pickling, baking and blasting rooms and sandblasting rooms.
Application Scenarios | Main protection design | Key Materials and Structures | Optional Replacement Program | Maintenance costs |
Acid Cleaning Room | 304 stainless steel plate + stainless steel hinges on the inside; built-in PVC door curtain | Stainless steel inside + color steel outside; heat insulation is high-density PU foam | Rigid Rapid Door + PVC Protection Layer | Low (PVC replacement is cheap) |
Drying and Blasting Room | Integrated explosion-proof electric control system; high sealing | High-sealing color steel or aluminum alloy door panel + explosion-proof equipment | Fire-Rated Rolling Door (Explosion-Proof + High Sealing) | Medium |
Sand Blasting Room | PVC door curtain on the inside of the door panel; high-strength metal and anti-abrasion coating application scenarios | High-strength metal door panel + anti-abrasion treatment + PVC protective layer | Rigid Rapid Door + Built-in PVC Protection Layer | Low |
Sourcing and Implementation Strategy
Customization Capability: Select suppliers with customized design capability to ensure that sectional door solutions can be tailored to specific industrial environments (pickling, baking, sandblasting).
Supplier certification: Focus on suppliers with relevant international certifications (e.g. CE, ISO) as well as technical qualifications for anti-corrosion, anti-explosion, and anti-wear technologies.
Long-term maintenance: Establish a maintenance and periodic inspection program to ensure the long-term stable operation of the door system and reduce the risk of sudden failure.
Consideration of replacement programs: Consider the replacement programs for different door types when making decisions. And choose the optimal combination based on actual application scenarios and technical requirements.
Installation and Maintenance Suggestions Maintenance Costs
定期维护
Daily inspection: clean the track and check the wear and tear of the nylon pulleys against the 2.0mm galvanized track.
Quarterly maintenance: Test the button spring (82B or 60Si2Mn) for signs of fatigue to ensure that the anti-pinch function is normal. Check the integrity of the sealing strip (EPDM rubber).
Annual Replacement: Regularly replace aged PVC door curtains and sealing materials to ensure that the protective effect is not reduced.
Operation record: Record about 10 times of opening and closing per day to ensure that the equipment is operated for 30 minutes between each operation, which is conducive to heat dissipation and mechanical recovery.
Comprehensive summary of sectional door customization solutions in special industrial environments
This article details sectional door customization solutions in special industrial environments such as pickling rooms, drying and spraying rooms and sand blasting rooms.
The pickling room solution offers double protection with a 304 stainless steel inner panel and PVC door curtains to effectively resist corrosion from the pickling solution.
The drying and blasting room solution ensures a safe working environment through explosion-proof electric control and high sealing design.
The sand blasting room program combines a built-in PVC door curtain with a reinforced metal structure to reduce the damage caused by the impact of sand blasts.
In addition, high-speed roller shutter doors and fireproof fast doors are also provided as replacement programs for enterprises to choose flexibly according to the actual application scenarios. Through scientific selection, customized design, and regular maintenance. Enterprises can greatly extend the service life of the sectional door system. Improve production safety and effectively reduce maintenance and operating costs.
常见问题
Q1: How does sectional door prevent corrosion of pickling solution in pickling room?
A: 304 stainless steel inner plate and stainless steel hinges are used. And PVC door curtains are installed on the inner side to form double protection to prevent the pickling water from directly contacting the metal parts.
Q2:What are the explosion-proof measures of the integrated drying and spraying room?
A: Integrated explosion-proof electric control system and high sealing design, together with explosion-proof materials and sealing strips, ensure that dust and flammable gases do not enter the door body during the spraying operation.
Q3:How to reduce the wear and tear of sectional door in sand blasting room?
A: Add a PVC door curtain on the inside of the metal door plate with high-strength metal and anti-wear coating to block the direct impact of the sandblast and reduce the long-term maintenance cost.
Q4:How to choose the combination of high-speed rolling door and sectional door in the replacement program?
A: In the pickling room and sand blasting room, the high-speed rolling door can provide faster opening and closing. But needs to add a PVC protective layer; while the traditional sectional door is more advantageous in the overall sealing and maintenance convenience, according to the actual production needs of flexible choice.